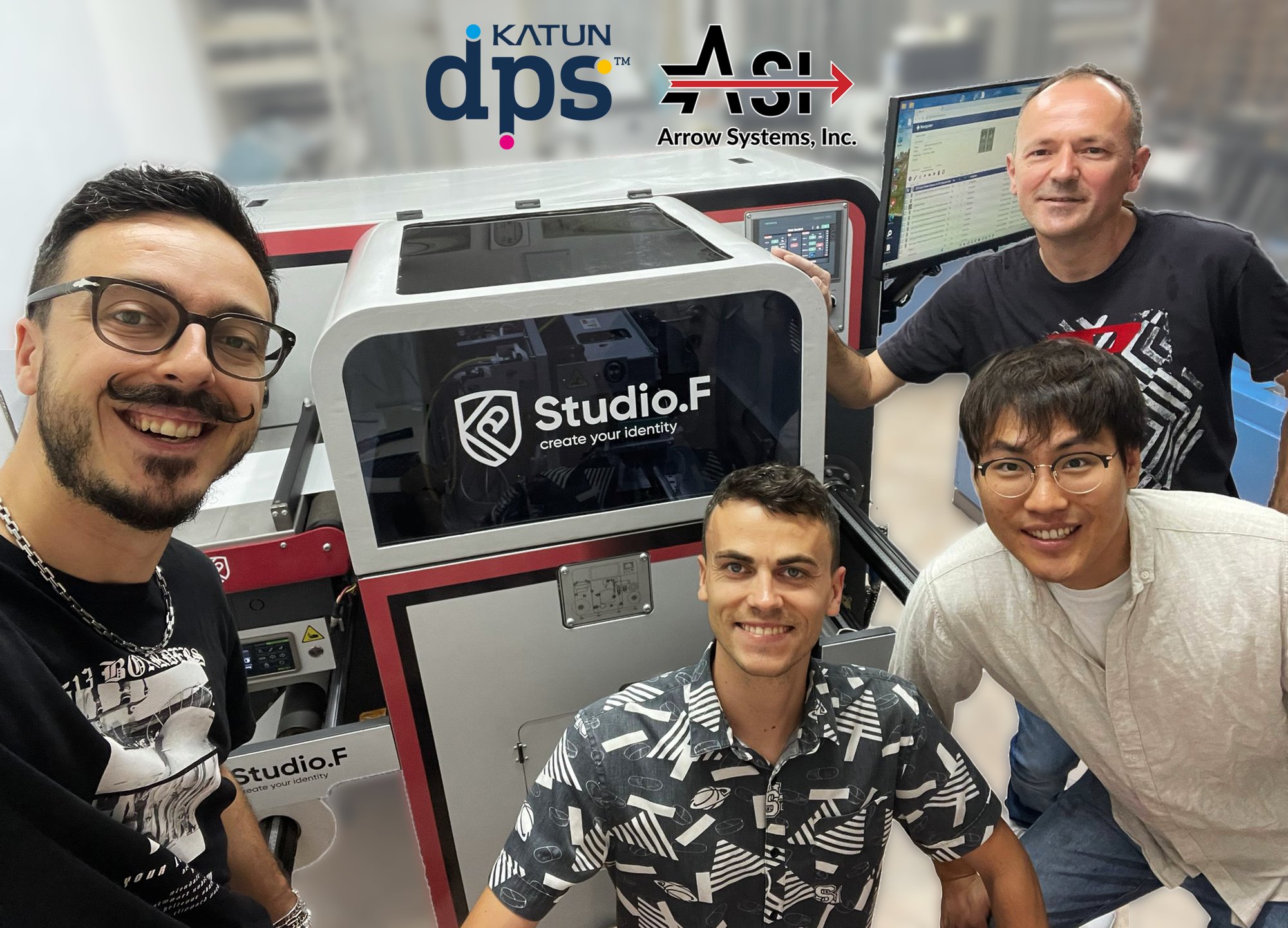
Hear it from Our Customers
In July 2024, we installed the ArrowJet Aqua 330R at Studio F's headquarters in Italy. Two months later, we caught up with Simone and Giacomo to hear about their experience with the installation, training and after-sales support provided by our expert team at Katun DPS® and Arrow Systems Inc. as well as their thoughts on the ArrowJet 330R printer itself. Curious about what they had to say? Keep reading to find out how Studio F's firsthand experience with Katun DPS® and its products went.
Overview
Q: Can you briefly share your overall experience with our machine and the installation process?
As a first impact, the ArrowJet Aqua 330R impressed us positively with its industrial design and solid construction. During installation we immediately noticed how well-designed and robust it was. The machine was able to print on different types of primed media with excellent print quality, which was one of our main needs. The installation process was relatively simple and well supported by the technical team who provided all the necessary instructions and guided us step by step. Overall, the first impact is definitely positive but it will be the long term that gives a definite answer about its actual reliability and performance.
Initial Need and Decision
Q: What specific challenges or needs led you to consider purchasing an industrial roll-to-roll label printing machine such as the ArrowJet Aqua 330R?
We were looking for a reliable machine at the right price. For 15 years we relied on roll-to-roll technology with laser printing and then switched to Memjet VersaPass™ technology. However, we found the Versapass™ technology to be outdated and unreliable especially if certain quality standards were to be achieved. The need to improve the quality of our printing and ensure greater reliability prompted us to consider purchasing the ArrowJet Aqua 330R. This machine represents a significant technological advancement for us by offering better performance and superior print quality.
Selection Process
Q: How did you discover our machine and what factors influenced your decision to choose it over other options?
We met Arrow Systems at the Labelexpo trade show in Brussels last year. It had immediately attracted us but at the time we were not yet ready to take on such an investment. We took our time to choose and sift through all the options available on the market. The Katun team was able to clearly explain to us all the pros and cons of the various options. In the end after careful consideration we had no doubts about choosing the ArrowJet Aqua 330R.

Expectations and Requirements
Q: What were your main expectations and requirements from the machine before you went ahead with the purchase?
For us, the most important thing is to offer the customer a good, quality product. Nowadays, with services offered online, you have to compete by offering a product and service that is up to par. We were looking for a machine that could print at least 200mm wide. With the ArrowJet Aqua 330R, now the maximum printable width is 330mm, giving us more possibilities and flexibility. In addition, we needed a machine that could print solid [high coverage colors]* without too much trouble, which other technologies struggle to do. This allows us to meet a wider range of customer requirements and maintain high quality standards.
Installation Experience
Q: How was the installation process at your location? Were there any challenges and how were they resolved?
The installation process of the ArrowJet Aqua 330R at our site was very satisfactory. The machine is very compact and, if it came into our company, I suppose it could be placed anywhere. We are a very small business and space optimization is key. We independently took care of connecting power and compressed air in an optimal way, which facilitated and increased the time we had with the technicians to study the machine in the best possible way. The two engineers, Elvir from Katun and Lee from Arrow Systems, were excellent throughout. Engineer Lee is without a doubt the best professional I have seen in action. Both of them were ready to adjust and install the machine to the best of their ability, allowing us to take advantage of its full potential.
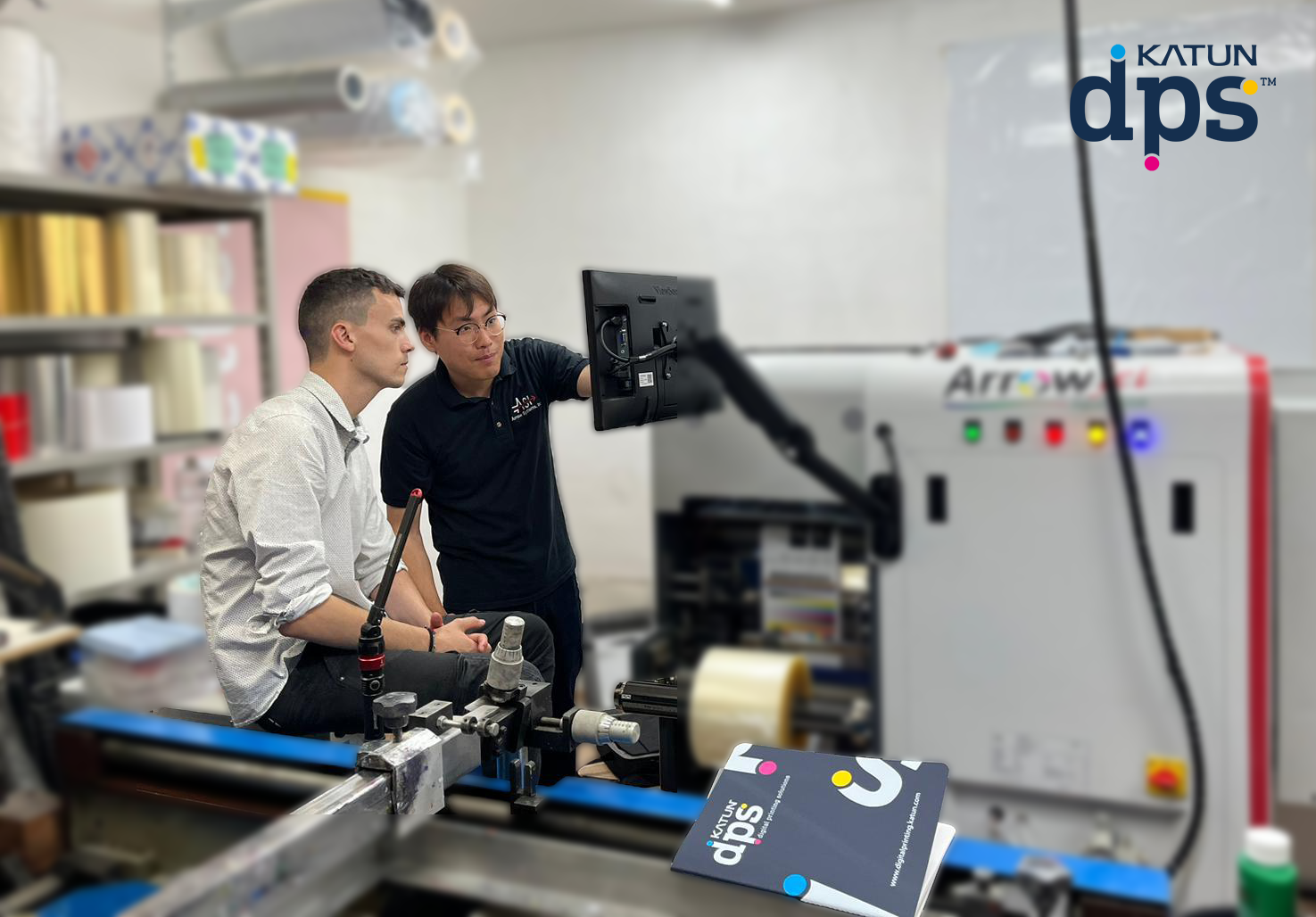
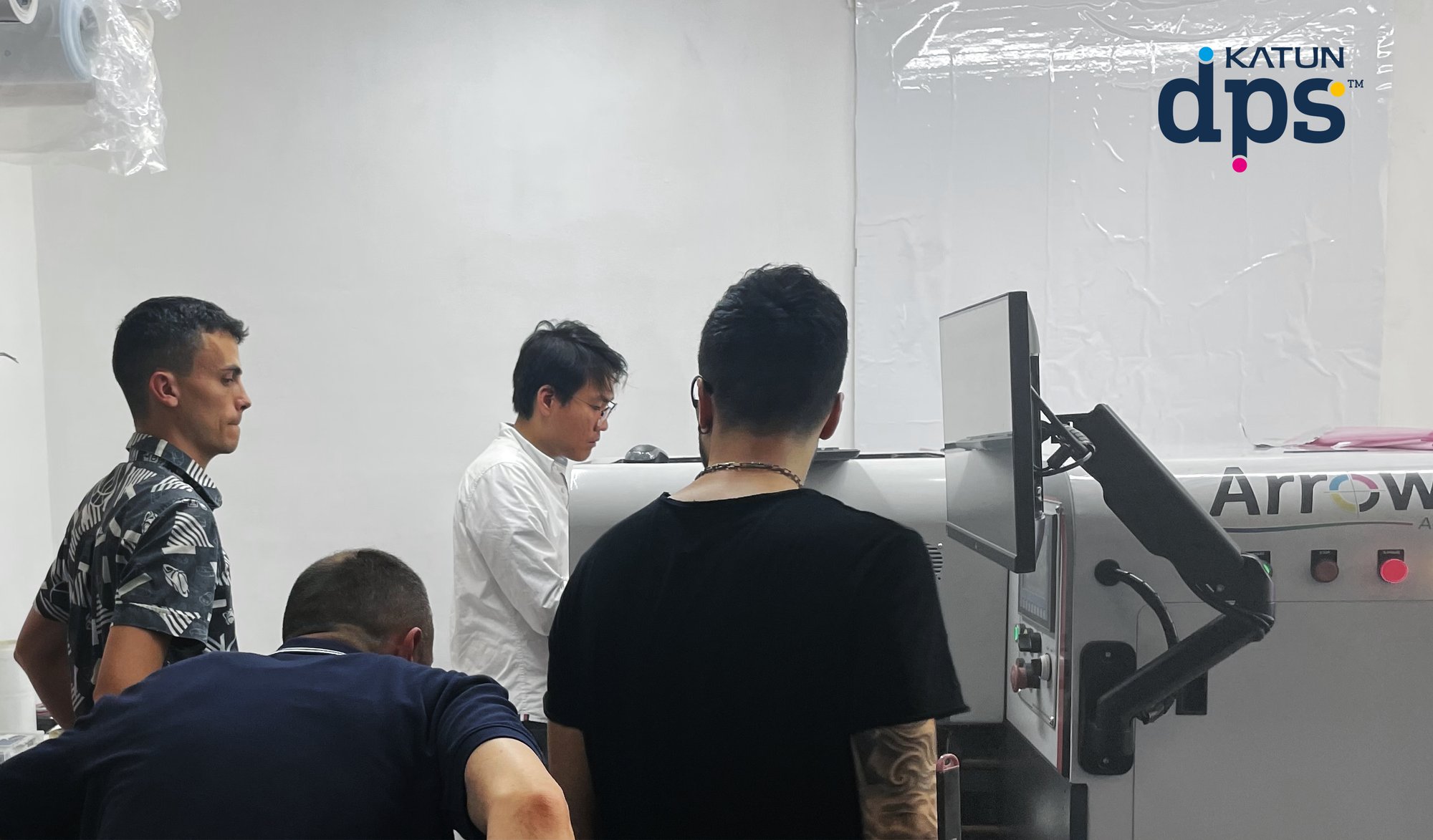
Training and Support
Q: How did you find the training and support provided by our team during and after installation?
Their team and the training was excellent, and after a week, we were comfortable using the printer independently. It was perhaps easier for us since we have already been in the industry for years, but the ArrowJet Aqua 330R is still a very intuitive machine. In the post-installation period from a month ago, the whole team is always ready to respond to doubts or requests, even outside their field. Their helpfulness and expertise have enabled us to face every challenge with peace of mind and to make the most of the machine's potential.
First Impressions
Q: What were your first impressions after the machine was installed and put into operation?
We were impressed by the speed of the ArrowJet Aqua 330R. It really is a rocket ship, although honestly speed is not our priority at the moment. What impressed us most is that regardless of whether it prints flat or fast, the quality of the print remains the same and is truly amazing. Maybe in the future its speed will be a potential we will take full advantage of, but for now we are very pleased with the consistent quality it manages to deliver.
Customer Satisfaction
Q: On a scale of 1 to 10, how satisfied are you with the machine and the overall experience? Could you explain your rating? How can we improve our services in the future?
We are very pleased with the machine and the overall experience, and
I would give it a rating of 9,5 out of 10!
The machine has been extremely effective and reliable in most aspects. However, the grade is not a 10 (yet) for one specific reason: we are currently working on ICC profiles with the Arrow and Katun engineer team to address some color match challenges. We are confident that, through this work, we will be able to improve color management and have custom ICC profiles ready to better suite our and our customers needs. We greatly appreciate the support we've received so far and are hopeful that, with these improvements, the machine will reach a 10 out of 10.
Future Outlook
Q: How do you see the impact of this machine on your business in the long term? Are there any future plans or expansions related to this new capability?
The new machine has had an extremely positive impact on our business. Because of its high quality and reliability, we are now able to significantly expand our production. The ability to print in larger quantities without compromising quality gives us new opportunities to meet growing demand and enter new markets. We have developed a number of plans to make the most of its capabilities. We are planning to expand our product line and explore new applications that we were not able to handle before-for example, that of flexible packaging.
Conclusion and Final Thoughts
Q: Is there anything else you would like to add about your experience or advice for potential buyers of label printers?
Based on my experience, I strongly recommend taking a few precautions before purchasing any machinery. First, ensure you're working with a provider who has the machine on hand—and better yet, see it in action. Don’t rely solely on brochures or virtual demos—test it with your own media under real conditions. Also, ask detailed technical questions to make sure you're dealing with knowledgeable industry professionals, not just salespeople trying to make a sale. Finally, make sure the quality of after-sales support and technical assistance is well-defined and satisfactory. In summary:
"a well-informed purchase and an accurate evaluation
of the machinery and supplier can make a big difference
in your experience and the long-term success of your business."
- Studio F
*Editor's note: This interview was originally in Italian and some alternations may have been conducted for translation.